Chemical Vapor Deposition (CVD) diamond coating has many excellent properties, such as high hardness, high thermal conductivity, low friction and low expansion coefficient. CVD diamond coated cutting tools are based on hard alloy materials and coated with CVD diamond film on the substrate of milling cutter, drill bit, blade and other tools to enhance cutting performance and effectively extend the tool life. It shows excellent performance in machining brittle materials such as graphite and carbon fiber composites, and in improving tool life and processing quality.
Coating diamond film on cutter products (such as end mills and drills) is beneficial to improving wear resistance, chip properties and prolonging tool life. The service life of CVD diamond coated cutting tools is 8-10 times longer than that of cemented carbide. The cutting speed of CVD diamond coated tools is 2~3 times higher than that of carbide tools. Its cutting edge is sharp and complete, and the friction coefficient is low. It can realize high speed and high precision machining of thin-walled graphite mold under high speed and low feed. At the same time, the service life of CVD diamond coated cutting tools is favored by graphite processing manufacturers in many cutting tool materials.
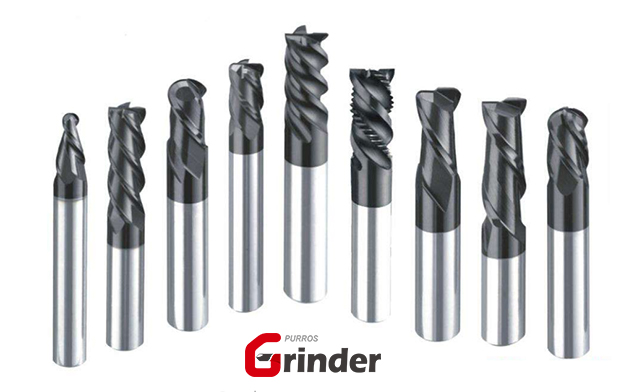
Chemical Vapor Deposition, CVD diamond film, CVD diamond coated tools, CVD diamond coated cutting tools
How to choose CVD diamond coated tools?
The choice of thickness of diamond coating is not “the thicker the better”. Its wear resistance and the quality of diamond coating are greater than that of thickness. The selection and application of diamond coated tools are mainly based on the properties of workpiece materials and the requirements of machining quality. For EDM graphite mold processing, the milling process is similar to the “grinding” process, which requires a large number of “micro-edges” on the surface of the tool and wear resistance, so we should choose the micro-diamond coating with large grain.
Nano-diamond coating should be selected in the finishing stage for the die used in ceramic processing, which requires high surface finish. In the aluminum alloy processing, “sticking tool” phenomenon is more serious than tool wear, at this time the wear resistance of the tool is relatively low, nano-diamond coating with low friction coefficient should be selected.
For carbon fiber composites, micro/nano composite diamond coatings should be used because of the strong abrasive wear resistance of the fiber material itself, which not only requires good wear resistance of the cutting tool, but also reduces the cutting force and cutting heat during the machining process.